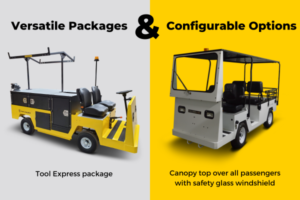
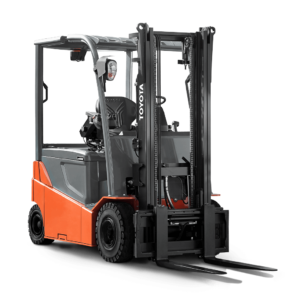
THE FULL LINE OF MATERIAL HANDLING PRODUCTS
Technolojkl; ;about the function of their warehouses, and give themselves a competitive advantage.
The issue with maintaining that competitive advantage is that sometimes a WMS no longer provides the best possible solution. However, some managers get so invested in them, they can’t tell that they’ve outgrown their system and that there are better solutions that could help them grow their success. So how do you know it’s time to move on from your current system?
1. The Warehouse Management System No Longer Fits Your Material Needs
In the context of a small timeframe, a WMS should take into account the material that is in your facility and allow you to make decisions about how to go about picking that material. But over time, material practices change, even within the same industry or business. Some WMS systems can fail to take into account changes, recommending storing and picking methods that no longer make sense given changes to materials. Ask yourself if the WMS is taking into account the full extent of the changes to the material in your facility (whether your business is changing, your industry is changing, or you’re scaling up). If it’s not, it might be time to move on.
2. The Warehouse Management System Cannot Integrate with Other Software Being Used in the Facility
Technology changes rapidly and sometimes disjointedly. Updates to partnered systems can quickly leave a piece of software behind, not because the software fails to perform its intended function, but because that software cannot integrate and share data with other systems. These older technologies, which are sometimes referred to as “legacy systems”, can block an operation from unifying its most important data sets. For example, if you experience an update to your Transportation Management System (the system that shows where your goods are located in the intermodal supply chain) and your WMS no longer communicates with it effectively, then you lose a holistic view of your operation. By the same token, if your WMS no longer communicates with your Labor Management System, you won’t have a good understanding of how material and throughput impact needed staff assignments. If your WMS is the logjam, it might be time to find a new one.
3. The Warehouse Management System is Hurting Customer and Supplier Relations
The bottom line is that technology should help improve your business relationships. A good WMS improves accuracy, decreases customer lead time, and, ultimately, drives those relationships that lead to repeat orders. It’s easy to see declining accuracy or decreased customer satisfaction as a problem of personnel or product. But if it’s a process that’s getting in the way, it’s time to assess your process systems like your WMS. The same is true from a supplier relations perspective. If your WMS can help your personnel be ready to receive quickly and efficiently, then your delivery partners can move onto their next order or task. If WMS errors means you mistime receiving and need to scramble, your supplier is also delayed, and the reputation of your business is damaged. It might be time to change WMS software.
All of these can be key indicators that it’s time to explore alternatives to your WMS. While doing so can be a large undertaking that includes new training and systems integration, it can be worth it to improve business practices. It would be useful to work with an expert warehouse advisor to help you assess software practices and provide outside advice.
Share this Post
Other Post
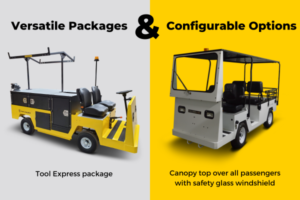
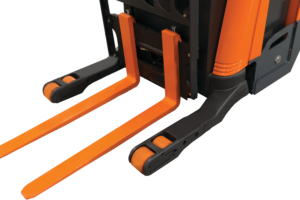
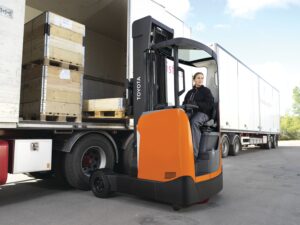
Toyota’s Moving Mast Reach Trucks: A Versatile Warehouse Solution
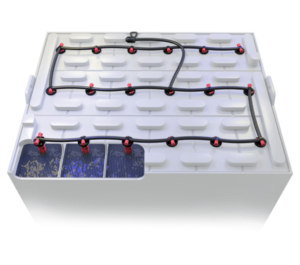
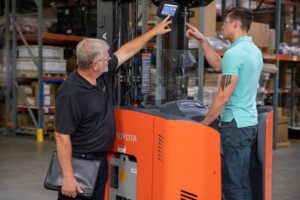
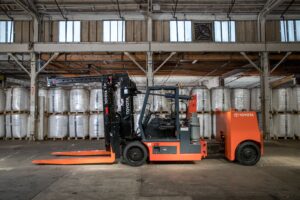